
MES
Manufacturing Execution Systems are the key to being more efficient by implementing Track & Trace, OEE/Downtime and SPC solutions to compete in a rapidly changing industrial environment. At Dean Systems we pride ourselves in helping our clients navigate the complex issues surrounding their MES deployment and business intelligence.
What is MES?
The acronym MES stands for Manufacturing Execution System. This software is powerful and helps supervisors track and monitor real time information when they need it to optimize efficiency. MES integrates all business systems with production infrastructure to help enhance operations. A few critical components to MES systems include Track & Trace, OEE/Downtime, and SPC Solutions.
Track and Trace: This piece of the MES system helps supervisors monitor the progress of a product through the processing and recording of each valuable benchmark. The gathered data relies on your ERP (Enterprise Resource Planning) and warehouse systems to provide product genealogy from the raw materials to shipping finished products to the customer.
OEE/Downtime Tracking: OEE is a universally accepted metric used to evaluate the effectiveness of manufacturing processes and equipment. OEE offers many significant benefits that help identify problems and room for improvement by breaking down the 3 factors that go into an OEE calculation availability * performance * quality. Each of these categories then allows for a more in depth look for improvements or correcting existing issues. Real time reporting also allows for enterprise wide monitoring of all scheduled runs as well as monitoring efficiencies by product.
SPC Solutions: Combines your process data with your quality control data. The process begins by collecting samples of data either in real-time or using past numbers. Analytical tools are created to help people make sense of the numbers that are being represented. The system will then provide control limits and scenarios that can alert supervisors of quality trends, adjustments that need to be made, and fix other issues.
Track and Trace
Industries like Food and Beverage, Manufacturing, and Aerospace all use Track and Trace to track raw materials throughout the production process. The system produces a genealogy graph of each step to provide valuable contextual data to the facility operators.
ERP and your warehousing systems are used to pull in raw material lot numbers allowing total visibility in all lots of the facility. At every step of the process from raw material to finished product , process data is stored and then displayed in an easy to follow format allowing operations group and executive team to know the precise point in the process that their run order is at with details on each step it has been through.
By having Track and Trace, supervisors are easily able to pull up production orders if there is a recall or a quality issue that needs to be addressed.
Downtime/OEE
The first important step in tracking the Downtime of your equipment is understanding what went wrong. In the perfect world, your equipment would run every day, all day. Unfortunately, that’s not the reality in most facilities. It’s expected to experience minor shutdowns, mechanical or electrical issues, machines becoming blocked, or other problems that prevent production.
These issues can be addressed and resolved by having a system that can organize and explain issues that come up. The data is collected in a way that highlights the most common downtime state of each cell to the company.
That’s where an OEE system comes in. When properly organized and operated, the OEE system helps you know what they can improve upon, whether performance, availability or quality. Downtime tracking exposes the problem or opportunity for improvement, and by integrating the OEE system, real-time and historical reporting will be readily displayed for management to understand what is causing the equipment downtime state.
OEE is a single number that’s given to represent the efficiencies of the processes. It can be calculated by Availability * Performance * Quality. Monitoring this over time as well as providing this data to a continuous improvement group can lead to enormous returns for all companies whether at the cell, line, area, site or enterprise levels.
Statistical Process Control (SPC)
SPC systems generate analytical tools to help make sense of the data that is presented to you. The system combines process data along with quality data to give the managers quality trend alerts and other analysis reports.
To begin, we take your quality control samples and the data that comes with each product. Some examples of this would include the product weight or product purity, and can go as in depth as needed.
Sample data is stored in a database and pulled out for analytical tool along with the process data to learn helpful control limits that should be set. When samples are collected in real-time, data is automatically used to improve quality during production.
SPC is extremely valuable for supervisors because it reduces waste, scrap, and re-work.
Why you need MES?
MES offers many firms the option to excel in their field of business. Many benefits of using MES include increased productivity, optimized workplace, efficient data capturing, real-time visibility of operations, and more. Material traceability is probably the most attractive benefit for companies that typically need to track each product. MES services that are offered must adhere to strict guidelines and regulations in order to be reliable, scalable and accurate.
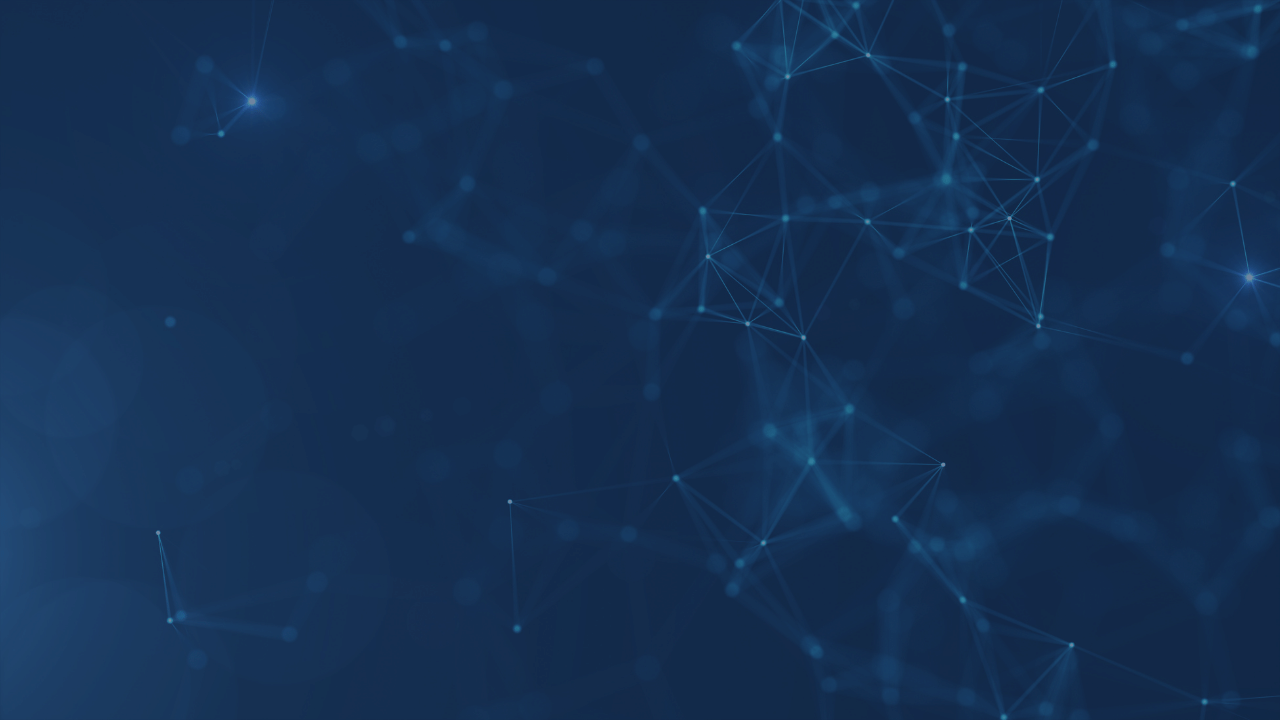
All systems deployed by Dean Systems
Follow the ISA 95 standard for MES systems. Following these standards and selecting the best technologies for the clients infrastructure allows for greater connectivity throughout the enterprise at all levels of the automation stack.
